All glass bottles are made of the same material, but in terms of craftsmanship, it is chosen based on the type of glass to be made. Glass is considered the most important material in the beverage industry, and every step in the glass bottle manufacturing process is also important.
The process of making glass may seem simple, but it encompasses many technologies that provide defect-free glass. Although the glass bottle manufacturing process comes in many forms, we will show you the glass bottle manufacturing process
Glass bottles are generally made of 7 to 12 different materials. The main materials used in the manufacturing process of glass bottles are silica sand, sodium carbonate, limestone, dolomite, feldspar, borax, barium, etc.
The most important raw material is silica because it determines the strength of the glass. The amount of silica can be selected according to the type of glass to be produced. The silica content is important because the melting point of glass is inversely proportional to it.
The manufacturing of the glass is a continuous process, so the batching processes will also occur continuously. Here the raw materials will be weighed and mixed, and then transferred into the hopper which is at the melting furnace.
Initially, the raw materials are feed to the hopers where it will get mixed and then transferred it into the furnace. Sometimes the conveyor belt consists of a magnet that will remove the magnetic materials. Once the raw material is mixed well, then it is feed into the furnace continuously using the batch process so that the composition of the material will be the same for all the processes.
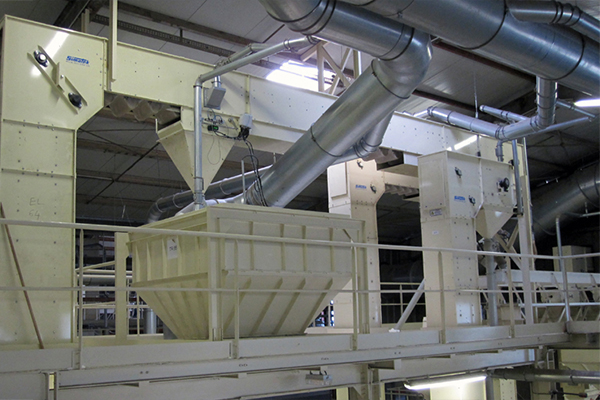
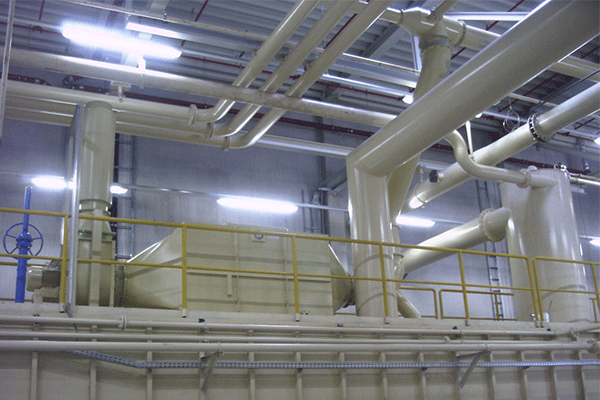
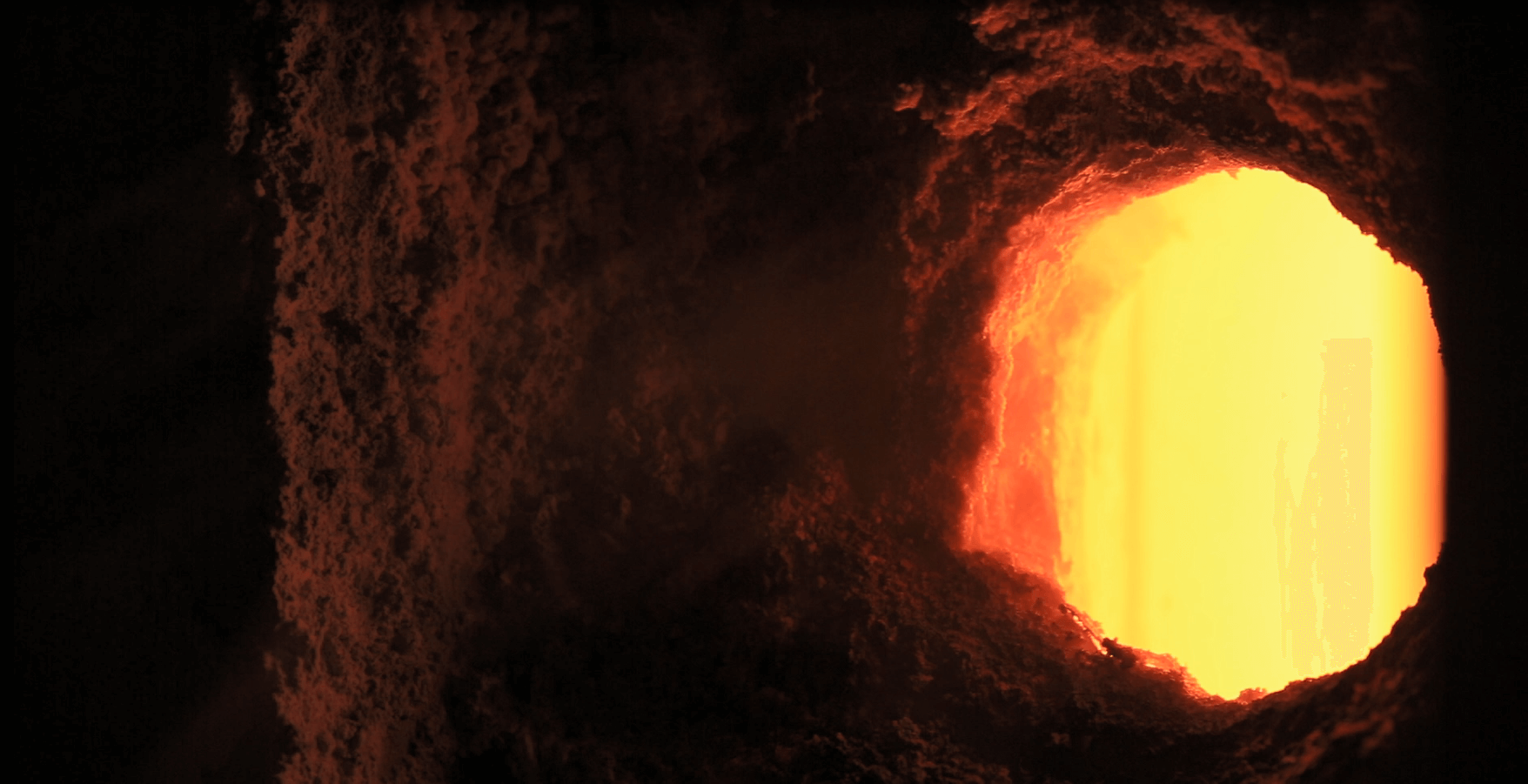
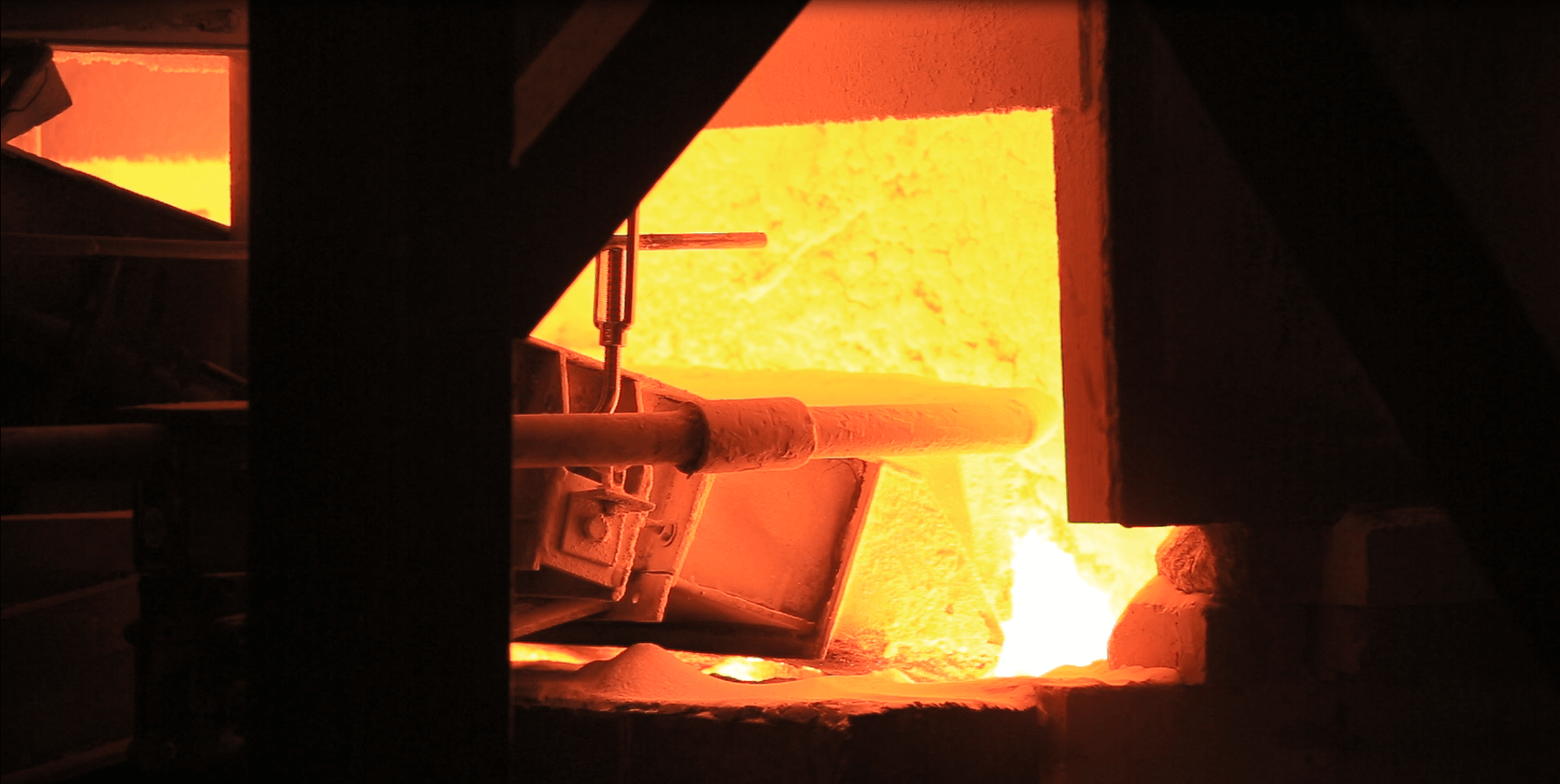
The next process is the feeding process, and in this stage, the glassblowers will be feed. The feeding of the glass gob should be done at an optimum temperature. The temperature is chosen based on the weight and shape of the bottle. Then the glass is fed into the glass-bottle forming machine through the feeder.
The feeders will have an opening at the end, and low shear panels control this opening. The speed of the sheer mass can be controlled and if you need a big size glass then the sheer speed should be less.
Once the elongated shape has been cut from the furnace, then the next step is to get the shape of the bottle. In the forming process, the forming machine will transfer the garbs into the container. Once the garbs are placed inside the mold, now air is blown into the forming machine, so that the shape will be obtained.
Once the shape is formed, it is removed from the mold. If you need to join any other shape to the glass, then you need to do it at this step, or else the glass will become hard, and then you need to melt the glass again.
Frosting will produce a high-quality glass, and the frosting can be done by sandblasting or and etching. The frosting can be done any kind of glass, and while working with acid you need to be careful.
If you are planning to glaze your glass, then glaze spraying is an effective process as it will spread the glaze evenly, and the glaze will get dried quickly.
Based on the customer’s requirement, the bottle will be packed accordingly. Also, the bottles are packed according to the destination, and then they will be stored in the warehouse or will get shipped to the customers.
The glass bottles will be wrapped in a cardboard box, and this box will contain multiple segments that have been separated by corrugated sheets. Mostly, the packaging will be an automatic process, so that any kind of damage can be avoided.